In today’s competitive business landscape, the quest for excellence is unending. Consumers demand products and services that meet or exceed their expectations consistently. To thrive, businesses must not only meet these expectations but also aim to surpass them. This is where Quality Management Systems (QMS) come into play. A QMS provides a structured approach to ensure quality in every aspect of an organization’s operations, leading to improved customer satisfaction, operational efficiency, and overall business performance.
What is a Quality Management System?
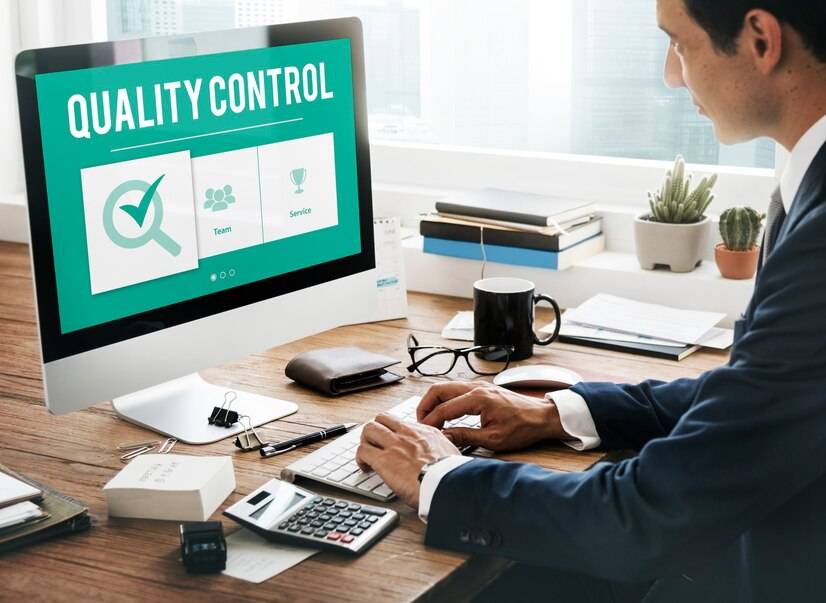
A Quality Management System (QMS) is a formalized system that documents processes, procedures, and responsibilities for achieving quality policies and objectives. It helps coordinate and direct an organization’s activities to meet customer and regulatory requirements and improve its effectiveness and efficiency on a continuous basis.
Key Components of a QMS
- Quality Policy and Objectives: The quality policy is a formal statement from management, closely aligned with the organization’s goals, which sets the overall intentions and direction regarding quality. Objectives are specific, measurable goals that are consistent with the policy.
- Quality Manual: This is a document that states the QMS policies and objectives and includes a description of the organization, its quality management system, and the roles and responsibilities of personnel.
- Procedures: Detailed instructions on how specific tasks should be carried out within the QMS to maintain quality standards. These are sometimes referred to as standard operating procedures (SOPs).
- Work Instructions and Records: These are detailed step-by-step guides that ensure every employee understands their role in maintaining quality. Records provide evidence that the procedures have been followed correctly.
- Process and Product Monitoring: Involves the ongoing assessment of both production processes and the end products to ensure quality standards are being met.
- Internal Audits: Regular reviews conducted internally to ensure compliance with the QMS and to identify areas for improvement.
- Corrective and Preventive Actions (CAPA): Processes for identifying the root causes of quality issues and implementing measures to prevent recurrence.
- Continuous Improvement: A commitment to constantly improve products, services, and processes using tools such as Six Sigma, Lean Manufacturing, and other quality methodologies.
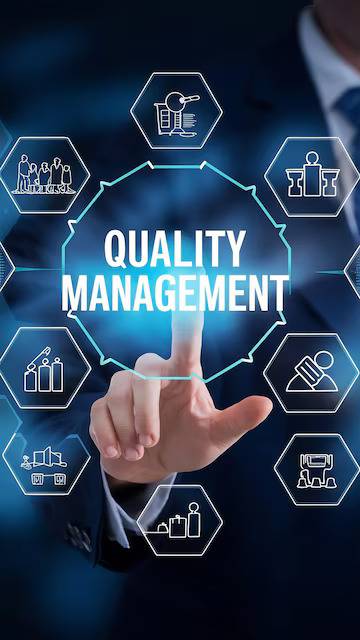
Importance of a Quality Management System
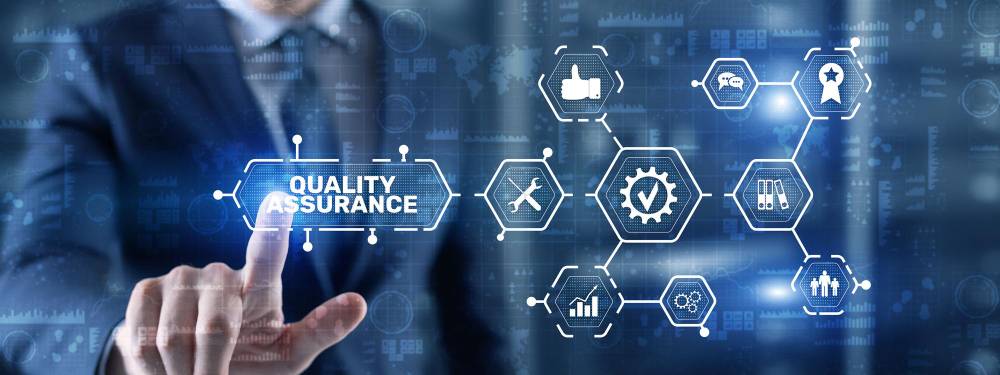
Implementing a QMS can bring numerous benefits to an organization, from enhancing customer satisfaction to streamlining operations. Here are some of the key reasons why a QMS is essential:
1. Consistent Product Quality
A QMS ensures that all processes within an organization are controlled and standardized, leading to consistent quality of products or services. This consistency builds trust with customers, who know they can expect the same level of quality every time they engage with the company.
2. Increased Customer Satisfaction
Satisfied customers are crucial to the success of any business. A QMS focuses on meeting customer needs and exceeding their expectations. By delivering high-quality products and services consistently, companies can enhance customer satisfaction and loyalty, leading to repeat business and positive word-of-mouth referrals.
3. Regulatory Compliance
Many industries are subject to stringent regulations and standards. A QMS helps organizations comply with these regulations by providing a framework for consistent quality management. Compliance not only avoids legal issues and penalties but also enhances the organization’s reputation and credibility.
4. Operational Efficiency
By standardizing processes and procedures, a QMS helps eliminate waste, reduce errors, and improve efficiency. It enables organizations to streamline their operations, making them more efficient and cost-effective. This leads to increased productivity and profitability.
5. Risk Management
A QMS includes mechanisms for identifying, assessing, and mitigating risks that could impact product quality and customer satisfaction. By proactively managing risks, organizations can prevent potential issues from becoming significant problems, reducing the likelihood of product recalls, legal disputes, or damage to the brand’s reputation.
6. Continuous Improvement
One of the core principles of a QMS is the commitment to continuous improvement. By regularly reviewing processes and performance, organizations can identify areas for improvement and implement changes that enhance quality and efficiency. This ensures that the organization is always evolving and adapting to changing market demands and customer expectations.
Types of Quality Management Systems
There are various QMS frameworks that organizations can adopt depending on their industry, size, and specific needs. Some of the most widely recognized and adopted QMS frameworks include:
1. ISO 9001
ISO 9001 is one of the most widely recognized QMS standards globally. It provides a framework for establishing, implementing, maintaining, and improving a quality management system. ISO 9001 is based on several quality management principles, including a strong customer focus, the involvement of top management, a process approach, and continual improvement.
2. Six Sigma
Six Sigma is a data-driven approach to improving quality by identifying and eliminating defects in processes. It focuses on reducing variability and improving process control to achieve near-perfect quality. Six Sigma uses a set of quality management methods, including statistical tools, and creates a special infrastructure of people within the organization (Black Belts, Green Belts, etc.) who are experts in these methods.
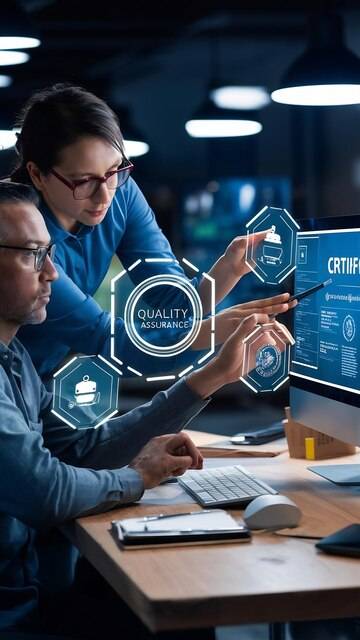
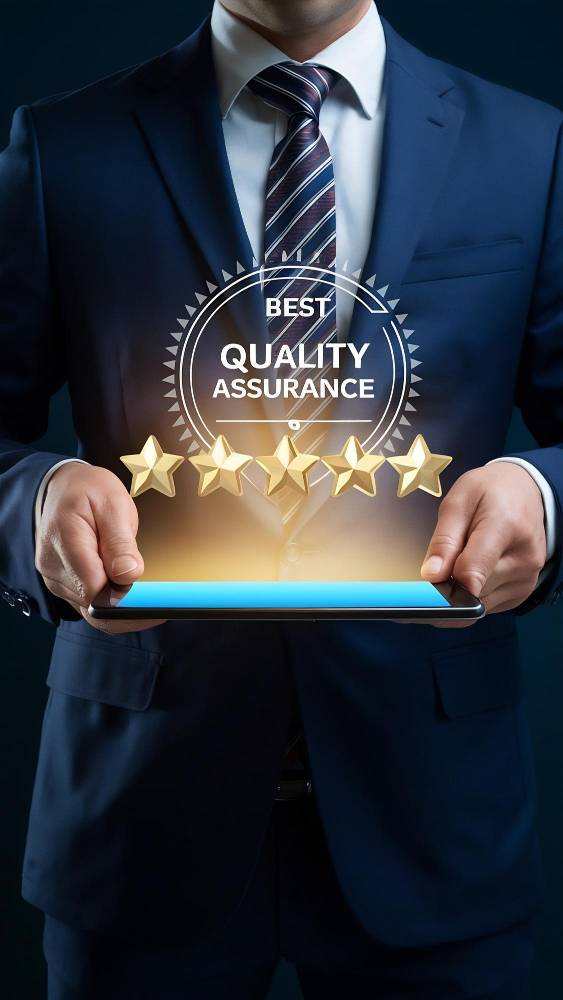
3. Total Quality Management (TQM)
Total Quality Management is a holistic approach to long-term success through customer satisfaction. TQM involves all members of an organization in improving processes, products, services, and the culture in which they work. It emphasizes customer-focused quality as the key to achieving and maintaining high standards.
4. Lean Manufacturing
Lean Manufacturing is a production method aimed at reducing waste within manufacturing systems while simultaneously maximizing productivity. Lean aims to create more value for customers with fewer resources. It focuses on improving the overall efficiency and quality of processes.
5. Capability Maturity Model Integration (CMMI)
CMMI is a process level improvement training and appraisal program. It helps organizations improve their processes and can be used to guide process improvement across a project, a division, or an entire organization. CMMI is particularly popular in software development and engineering.
Implementing a Quality Management System
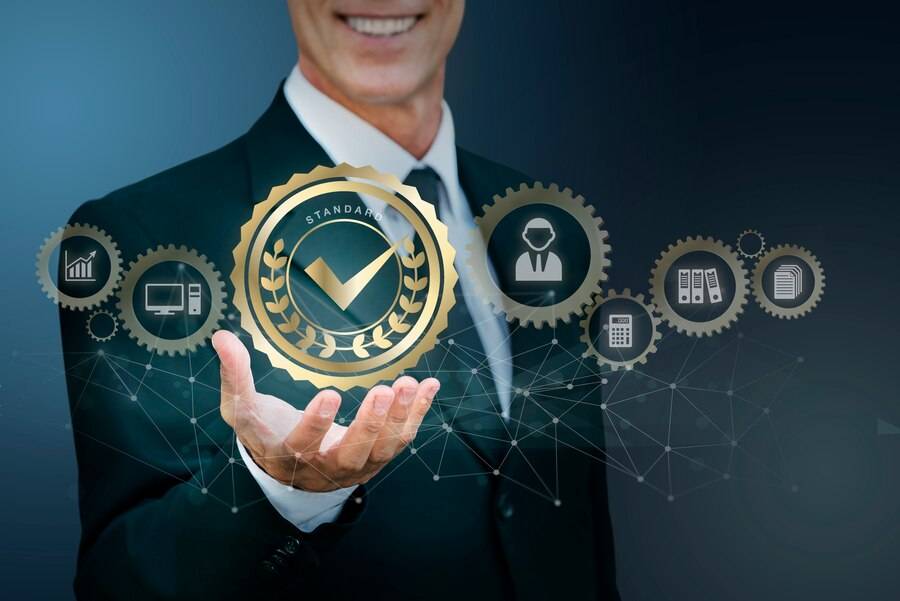
Implementing a QMS is a significant undertaking that requires commitment, planning, and resources. Here’s a step-by-step guide to implementing a successful QMS:
1. Define the Quality Policy and Objectives
The first step is to define the organization’s quality policy, which outlines its commitment to quality and continuous improvement. Quality objectives should be specific, measurable, achievable, relevant, and time-bound (SMART). These objectives align with the quality policy and provide direction for the QMS.
2. Identify Key Processes
Identify the key processes within the organization that impact product quality and customer satisfaction. This includes manufacturing processes, service delivery, customer support, and any other processes critical to quality. Understanding these processes is essential for developing procedures and work instructions.
3. Develop Procedures and Work Instructions
Document the procedures and work instructions for each key process. These documents should be clear, concise, and easily accessible to employees. Procedures outline the steps required to carry out a specific process, while work instructions provide detailed guidance on how to perform specific tasks.
4. Establish Performance Metrics
Performance metrics are used to measure the effectiveness of the QMS and identify areas for improvement. These metrics should be aligned with the quality objectives and provide meaningful insights into process performance, product quality, and customer satisfaction.
5. Train Employees
Training is a critical component of QMS implementation. Employees must understand the importance of quality, their roles within the QMS, and how to carry out their tasks according to the documented procedures. Ongoing training ensures that employees remain knowledgeable and capable of maintaining quality standards.
6. Conduct Internal Audits
Regular internal audits are essential for ensuring compliance with the QMS and identifying areas for improvement. Audits should be conducted by trained auditors who are objective and impartial. The audit findings provide valuable feedback for improving processes and enhancing the QMS.
7. Implement Corrective and Preventive Actions (CAPA)
When non-conformities or quality issues are identified, corrective and preventive actions must be taken to address the root causes and prevent recurrence. The CAPA process involves identifying the issue, analyzing the root cause, implementing corrective actions, and monitoring the effectiveness of those actions.
8. Review and Improve
Continuous improvement is a fundamental principle of a QMS. Regularly review the performance of the QMS, using the data collected from performance metrics, audits, and customer feedback. Identify areas for improvement and implement changes to enhance the effectiveness of the QMS.
Overcoming Challenges in QMS Implementation
Implementing a QMS can be challenging, especially for organizations that are new to quality management. Some common challenges include:
1. Resistance to Change
Employees may resist changes to established processes and procedures. To overcome this resistance, it is important to communicate the benefits of the QMS clearly and involve employees in the implementation process. Change management techniques can also help facilitate a smooth transition.
2. Lack of Management Commitment
Management commitment is crucial for the successful implementation of a QMS. Without the support and involvement of top management, the QMS may lack the necessary resources and authority to be effective. Management must lead by example and demonstrate their commitment to quality.
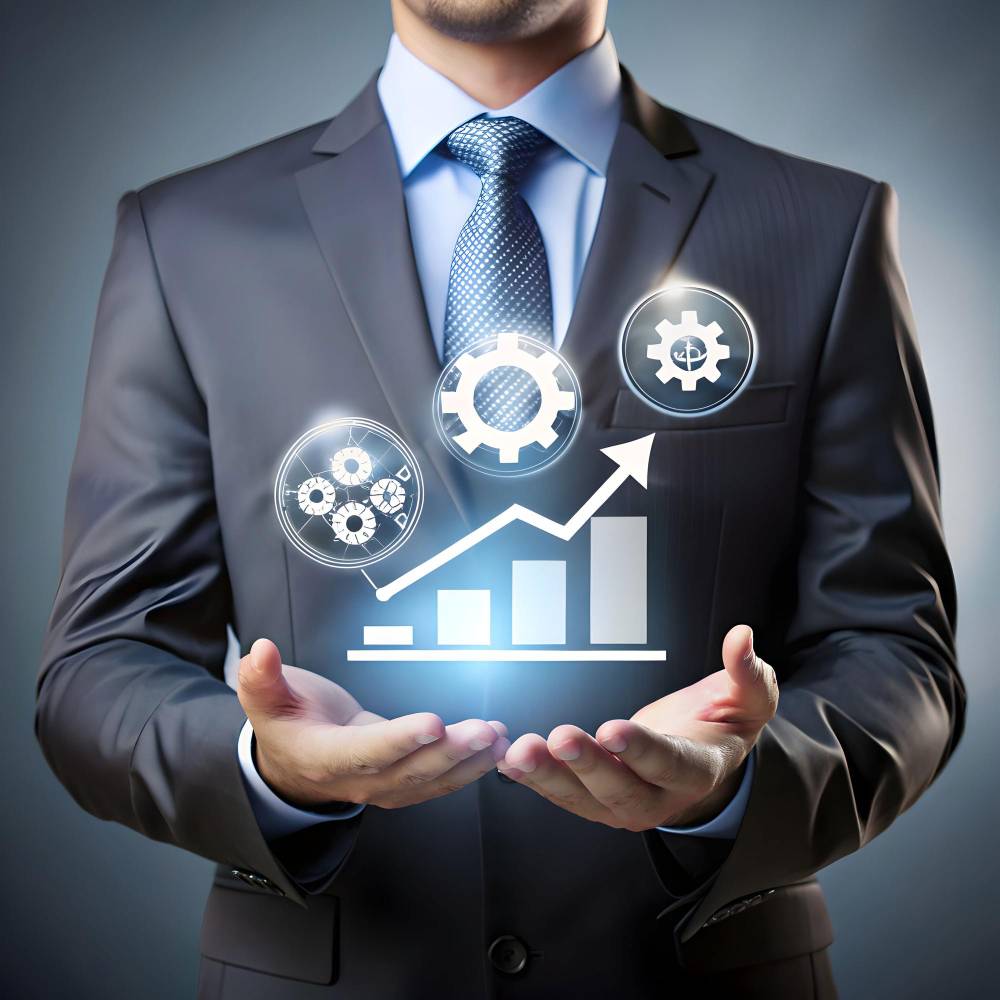
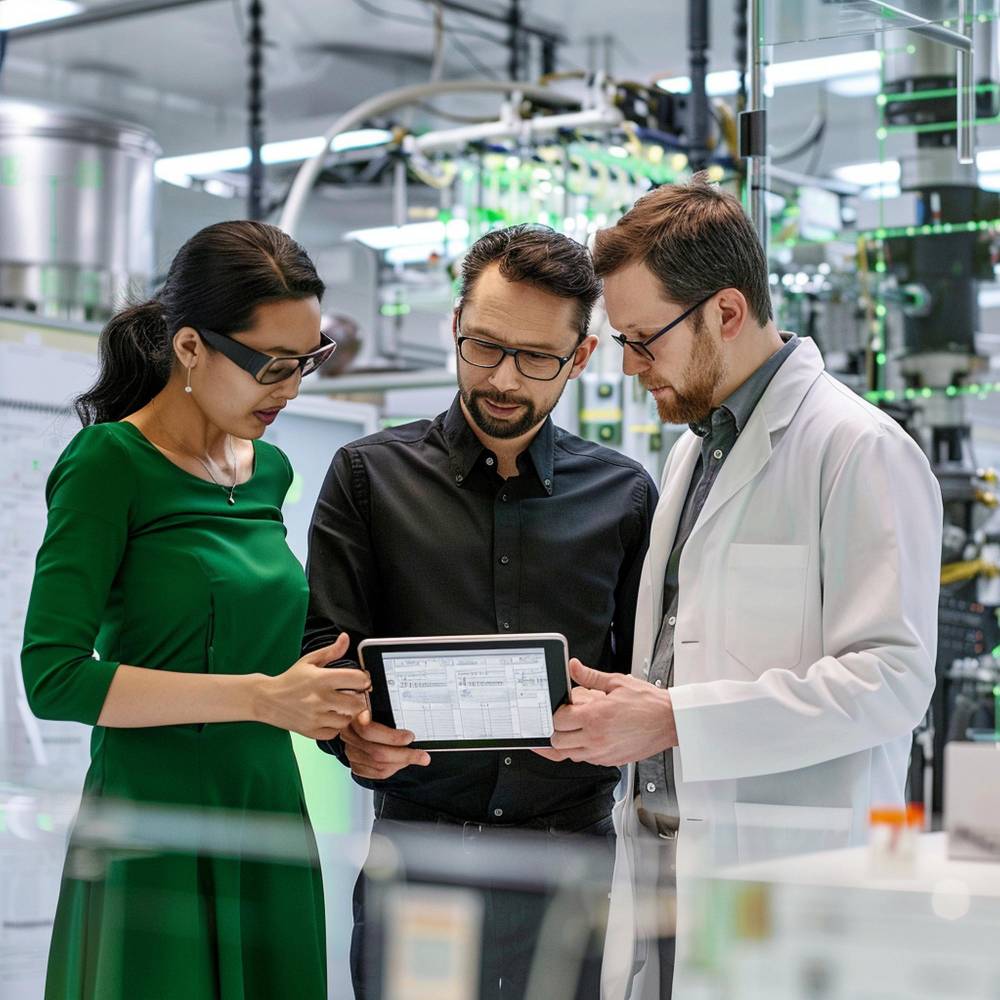
3. Insufficient Resources
Implementing a QMS requires time, effort, and resources. Organizations may face challenges in allocating the necessary resources for training, documentation, and auditing. It is important to prioritize quality management and allocate sufficient resources to ensure the success of the QMS.
4. Inadequate Training
Employees need the knowledge and skills to carry out their roles within the QMS effectively. Inadequate training can lead to misunderstandings, errors, and non-compliance. Invest in comprehensive training programs to ensure that all employees understand their responsibilities and are capable of maintaining quality standards.
The Role of Technology in Quality Management
Technology plays a significant role in modern quality management. Software tools and digital platforms can streamline QMS processes, improve data accuracy, and enhance communication. Some key technologies used in quality management include:
1. QMS Software
QMS software provides a centralized platform for managing quality processes, documents, audits, and corrective actions. It automates routine tasks, provides real-time data, and facilitates collaboration across the organization.
2. Data Analytics
Data analytics tools enable organizations to analyze quality data, identify trends, and make data-driven decisions. By leveraging data analytics, organizations can gain valuable insights into process performance and identify areas for improvement.
3. Mobile Technology
Mobile technology allows employees to access QMS documents, record data, and perform audits from mobile devices. This increases flexibility, enhances real-time data collection, and ensures that quality management is integrated into daily operations.
4. Cloud Computing
Cloud-based QMS solutions provide scalability, accessibility, and security. They allow organizations to store and manage quality documents and data in a secure cloud environment, making it easy to access and share information across multiple locations.
Conclusion
Quality Management Systems are essential for ensuring product and service excellence in today’s competitive market. By implementing a robust QMS, organizations can enhance customer satisfaction, improve operational efficiency, and achieve sustainable growth. A commitment to quality is not just about meeting standards; it is about exceeding customer expectations and continuously striving for excellence.
In a world where quality can be the key differentiator, a well-implemented QMS provides the foundation for long-term success. It instills a culture of continuous improvement, empowers employees to take ownership of quality, and positions the organization as a leader in its industry. Quality management is not a one-time project but an ongoing journey that requires dedication, collaboration, and a relentless pursuit of excellence.