Inventory Control Strategies:
Balancing Stock Levels and Demand
Managing inventory effectively is crucial for the success of any business. Striking the right balance between stock levels and demand can minimize costs, maximize profitability, and ensure customer satisfaction. This comprehensive guide explores inventory control strategies that can help businesses maintain this balance, optimize operations, and drive growth.
Understanding Inventory Control
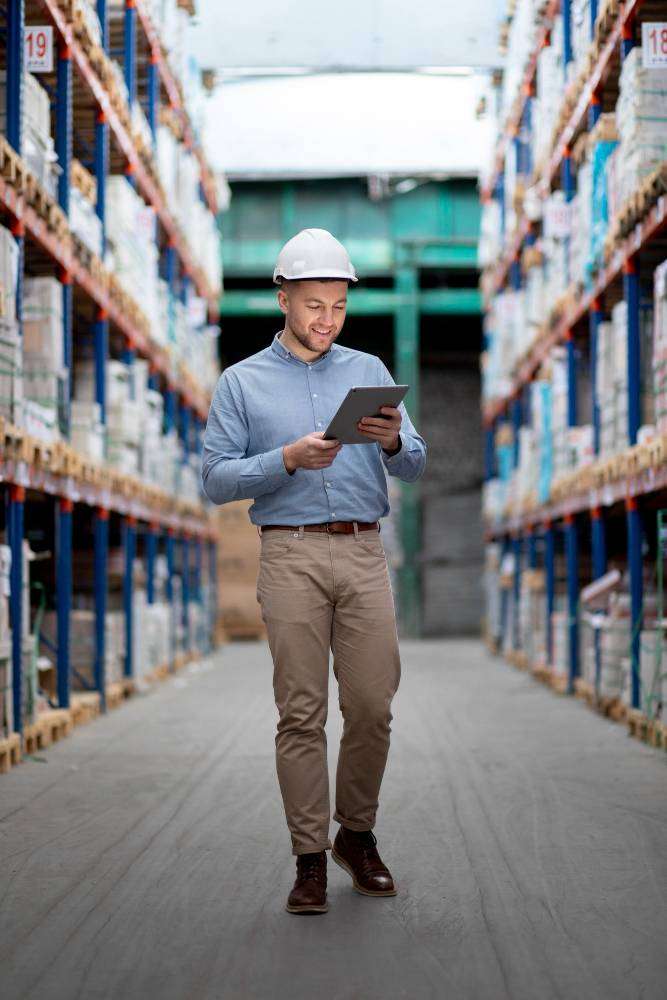
What is Inventory Control?
Inventory control refers to the process of managing a company’s inventory to ensure that the right amount of stock is available to meet customer demand while minimizing holding costs. Effective inventory control involves tracking inventory levels, forecasting demand, and implementing strategies to maintain optimal stock levels.
Importance of Inventory Control
- Cost Reduction: Proper inventory control reduces costs associated with excess inventory, such as storage, insurance, and obsolescence. It also minimizes stockouts, which can lead to lost sales and dissatisfied customers.
- Efficiency: Streamlined inventory processes enhance operational efficiency, ensuring that products are available when needed without overstocking.
- Customer Satisfaction: Meeting customer demand promptly leads to higher satisfaction levels and improved customer loyalty.
- Cash Flow Management: By maintaining optimal inventory levels, businesses can better manage cash flow, avoiding unnecessary capital tied up in excess stock.
Key Inventory Control Strategies
1. Just-In-Time (JIT) Inventory
Overview: JIT is a strategy where inventory is received only when it is needed for production or sales. This minimizes holding costs and reduces the risk of overstocking.
Benefits:
- Reduces storage costs and waste.
- Improves cash flow by minimizing capital tied up in inventory.
- Enhances efficiency and flexibility in production processes.
Implementation Tips:
- Develop strong relationships with reliable suppliers to ensure timely deliveries.
- Use demand forecasting tools to accurately predict inventory needs.
- Implement a robust inventory tracking system to monitor stock levels in real-time.
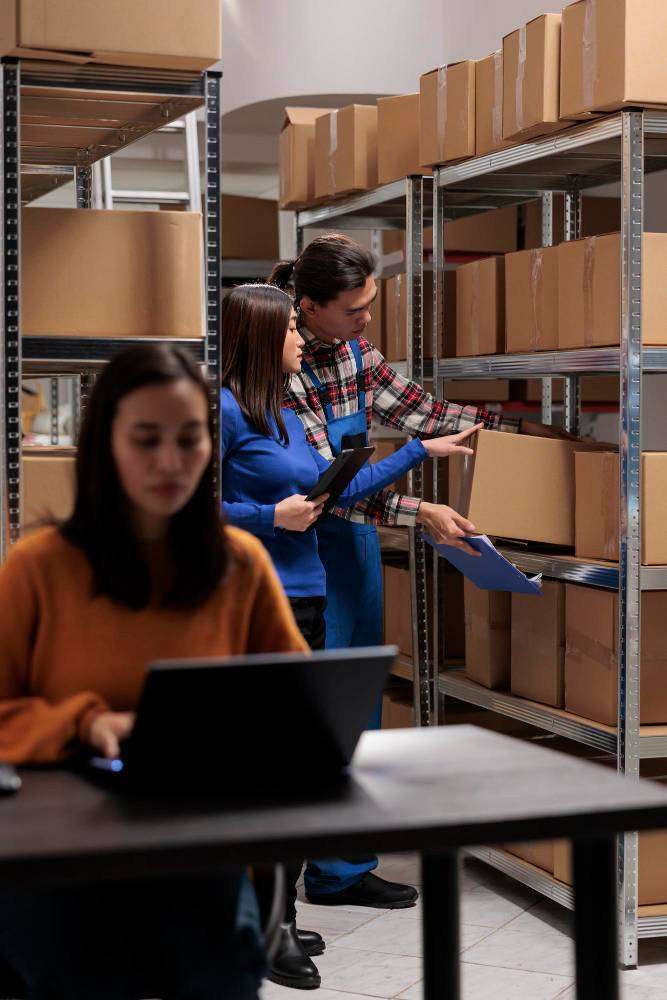
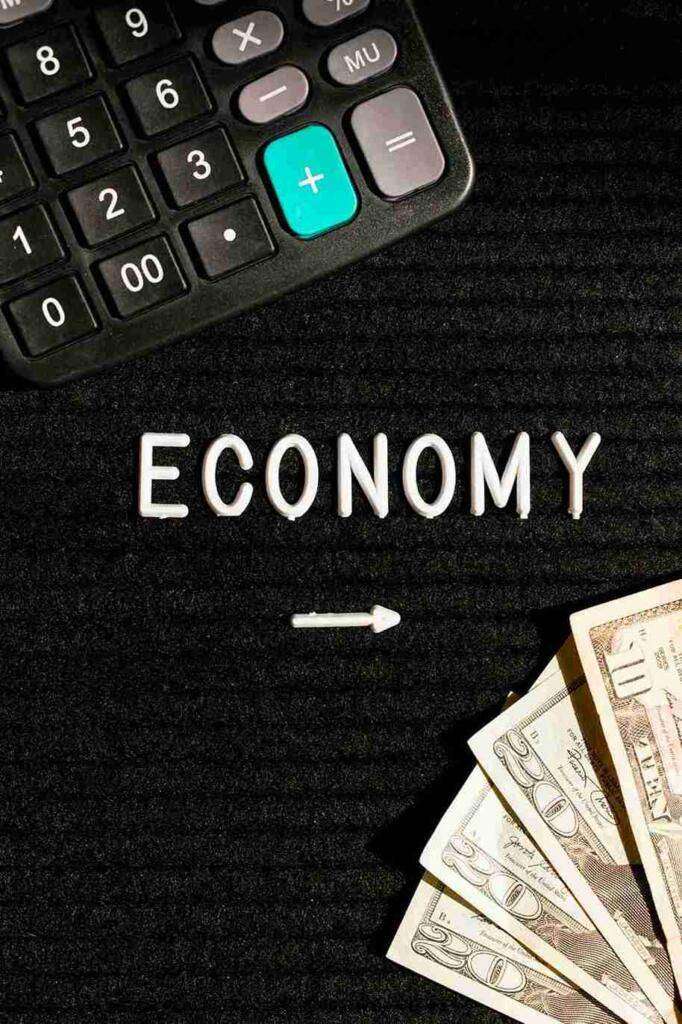
2. Economic Order Quantity (EOQ)
Overview: EOQ is a formula that determines the optimal order quantity to minimize total inventory costs, including ordering and holding costs.
Benefits:
- Balances ordering costs with holding costs.
- Reduces the frequency of orders and associated administrative expenses.
- Optimizes inventory levels to meet demand without overstocking.
Implementation Tips:
- Calculate EOQ using the formula: EOQ=2DSH\text{EOQ} = \sqrt{\frac{2DS}{H}}EOQ=H2DS, where DDD is annual demand, SSS is the ordering cost per order, and HHH is the holding cost per unit per year.
- Regularly update EOQ calculations to reflect changes in demand, ordering costs, and holding costs.
- Integrate EOQ with inventory management software for automated reordering.
3. ABC Analysis
Overview: ABC analysis categorizes inventory into three classes based on their value and importance: A (high-value), B (moderate-value), and C (low-value) items.
Benefits:
- Focuses management efforts on the most critical inventory items (A items).
- Improves inventory accuracy and control.
- Optimizes stock levels by prioritizing resources.
Implementation Tips:
- Conduct a thorough inventory analysis to classify items into A, B, and C categories.
- Apply stricter control and monitoring to A items, such as frequent cycle counts and tighter reorder points.
- Implement automated inventory management systems to handle B and C items efficiently.
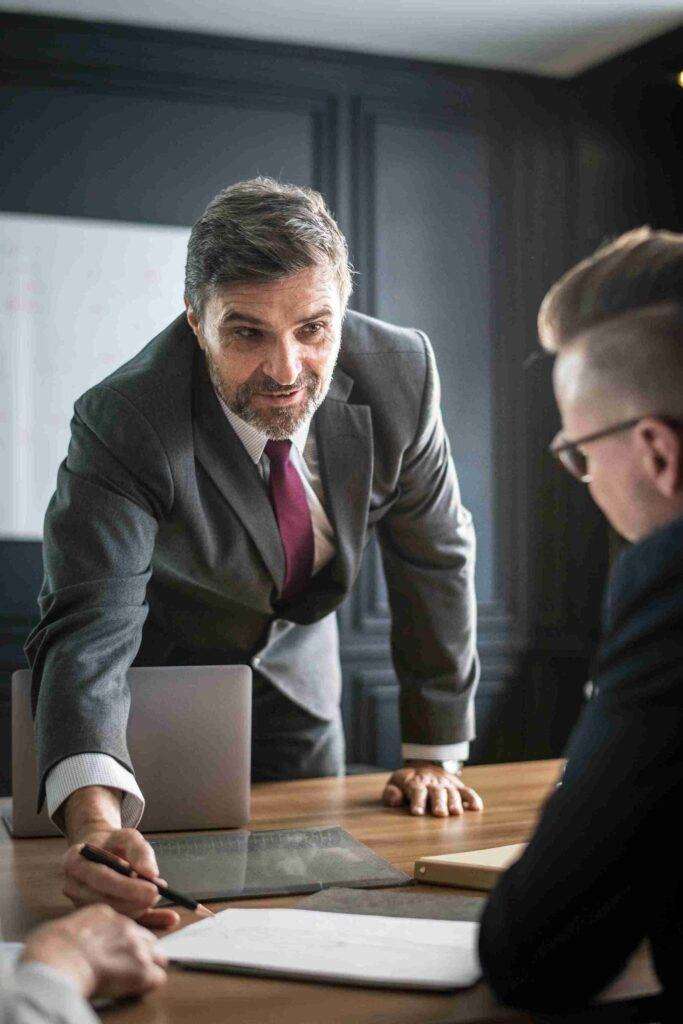
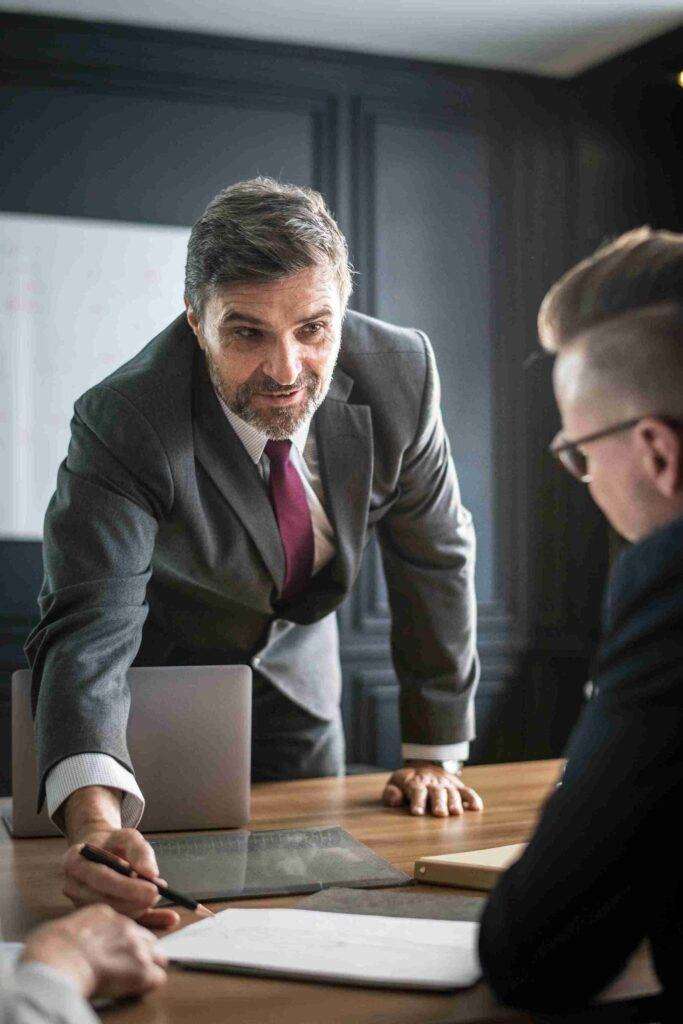
4. Safety Stock
Overview: Safety stock is an additional quantity of inventory held to protect against uncertainties in demand and supply.
Benefits:
- Prevents stockouts and ensures continuous product availability.
- Enhances customer satisfaction by meeting demand fluctuations.
- Reduces the impact of supply chain disruptions.
Implementation Tips:
- Calculate safety stock based on demand variability, lead time variability, and desired service levels.
- Use statistical models, such as the standard deviation of demand during lead time, to determine optimal safety stock levels.
- Regularly review and adjust safety stock levels based on changes in demand patterns and supply chain performance.
5. Reorder Point (ROP)
Overview: ROP is the inventory level at which a new order should be placed to replenish stock before it runs out.
Benefits:
- Ensures timely replenishment of inventory.
- Minimizes the risk of stockouts.
- Optimizes ordering processes.
Implementation Tips:
- Calculate ROP using the formula: ROP=Lead Time Demand+Safety Stock\text{ROP} = \text{Lead Time Demand} + \text{Safety Stock}ROP=Lead Time Demand+Safety Stock, where lead time demand is the average demand during the lead time period.
- Monitor inventory levels in real-time to trigger reorder points automatically.
- Integrate ROP with inventory management systems for efficient and accurate reordering.
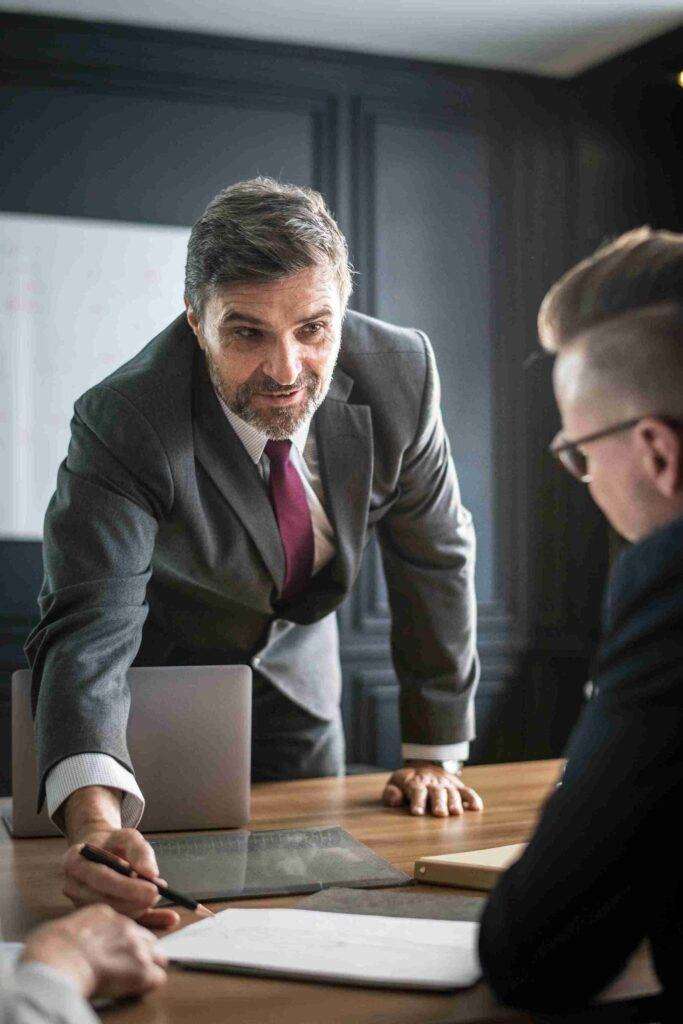
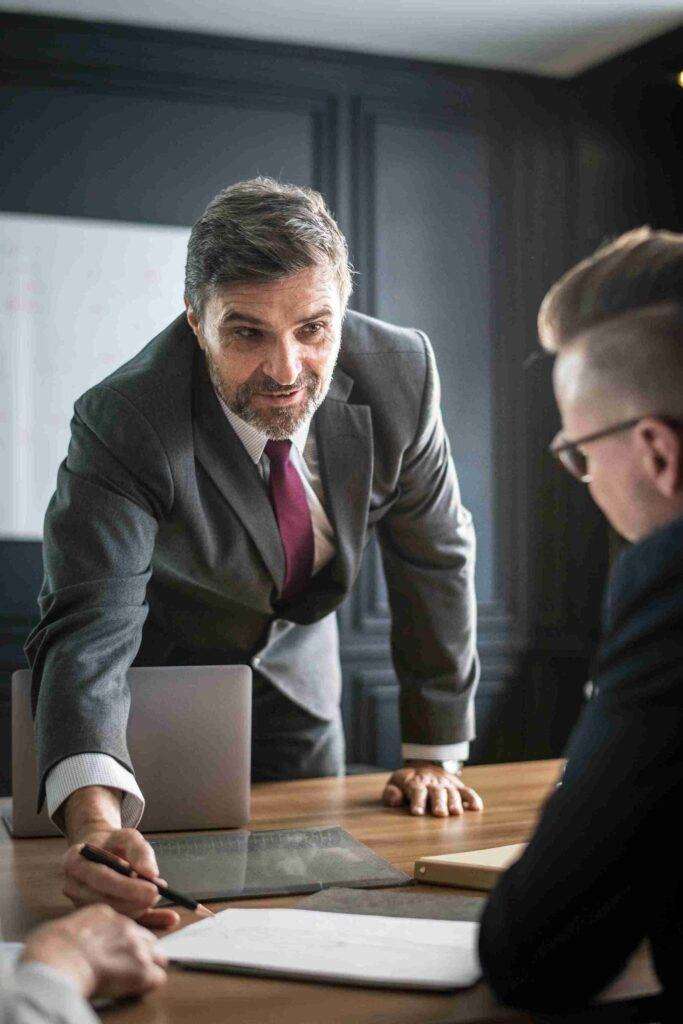
6. Vendor-Managed Inventory (VMI)
Overview: VMI is a collaborative strategy where suppliers manage inventory levels on behalf of the buyer, ensuring optimal stock levels are maintained.
Benefits:
- Reduces the buyer’s administrative burden and inventory carrying costs.
- Enhances supplier-buyer relationships and collaboration.
- Improves supply chain efficiency and responsiveness.
Implementation Tips:
- Establish clear agreements and performance metrics with suppliers.
- Share real-time sales and inventory data with suppliers for accurate inventory management.
- Use technology platforms to facilitate communication and data exchange between buyers and suppliers.
7. Demand Forecasting
Overview: Demand forecasting involves predicting future customer demand using historical data, market trends, and statistical models.
Benefits:
- Enables proactive inventory planning and management.
- Reduces the risk of overstocking and stockouts.
- Enhances decision-making and resource allocation.
Implementation Tips:
- Use a combination of qualitative and quantitative forecasting methods, such as moving averages, exponential smoothing, and regression analysis.
- Regularly update forecasts based on the latest market data and trends.
- Integrate forecasting tools with inventory management systems for seamless planning and execution.
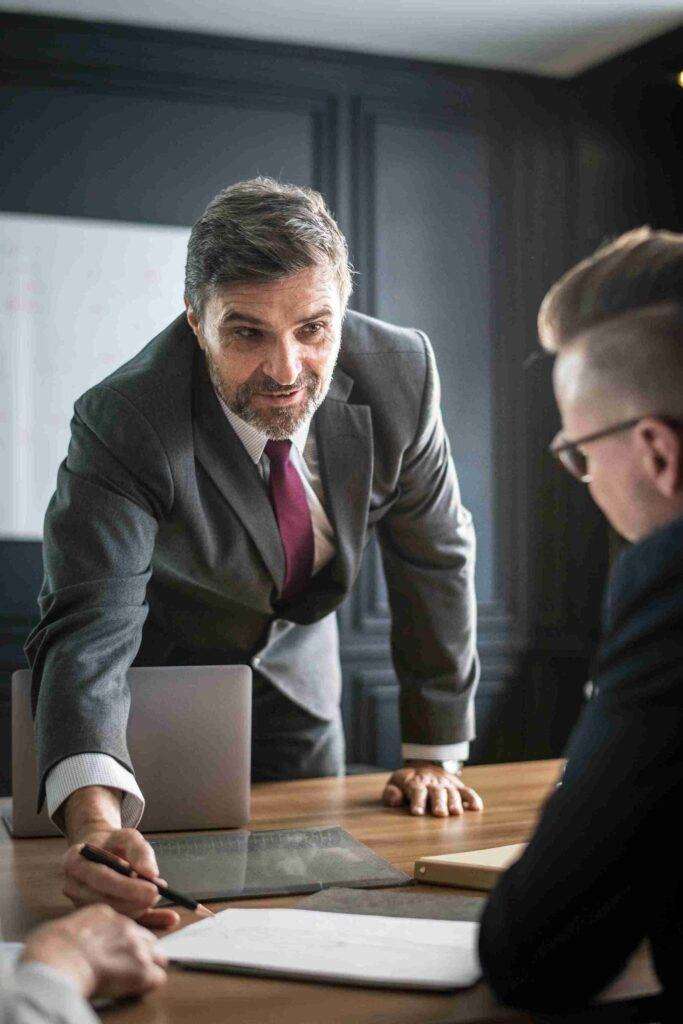
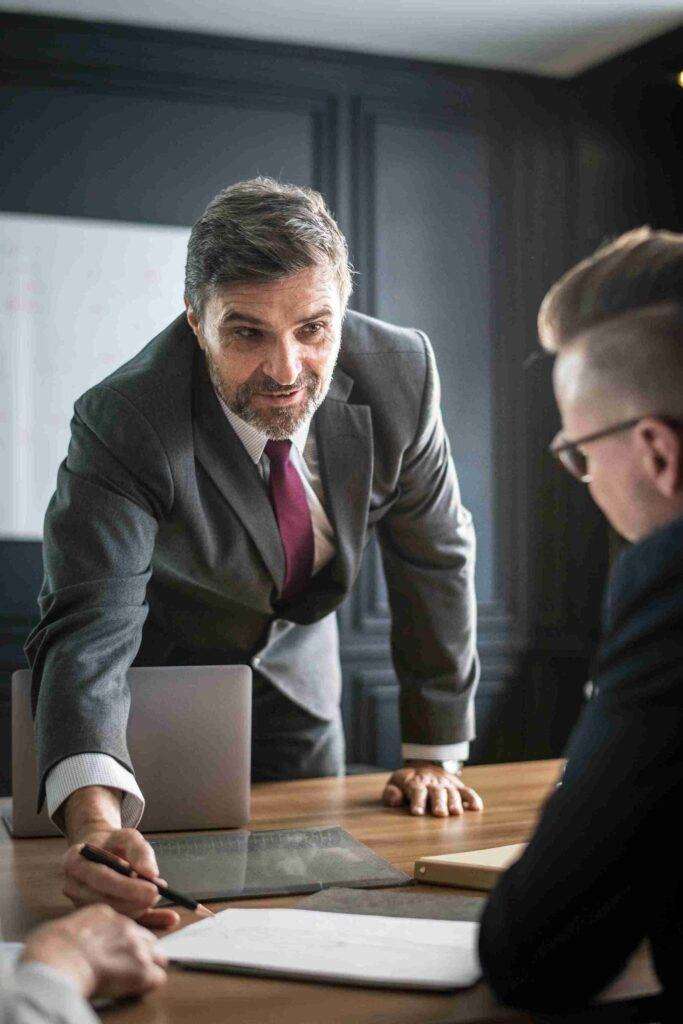
8. Inventory Turnover Ratio
Overview: The inventory turnover ratio measures how often inventory is sold and replaced over a specific period. A high turnover ratio indicates efficient inventory management, while a low ratio suggests overstocking or slow-moving items.
Benefits:
- Provides insights into inventory performance and efficiency.
- Helps identify slow-moving and obsolete items.
- Supports strategic decision-making for inventory optimization.
Implementation Tips:
- Calculate the inventory turnover ratio using the formula: Inventory Turnover=Cost of Goods SoldAverage Inventory\text{Inventory Turnover} = \frac{\text{Cost of Goods Sold}}{\text{Average Inventory}}Inventory Turnover=Average InventoryCost of Goods Sold.
- Analyze the turnover ratio by product category to identify areas for improvement.
- Implement strategies to increase turnover, such as promotions, discounts, and inventory liquidation.
Best Practices for Effective Inventory Control
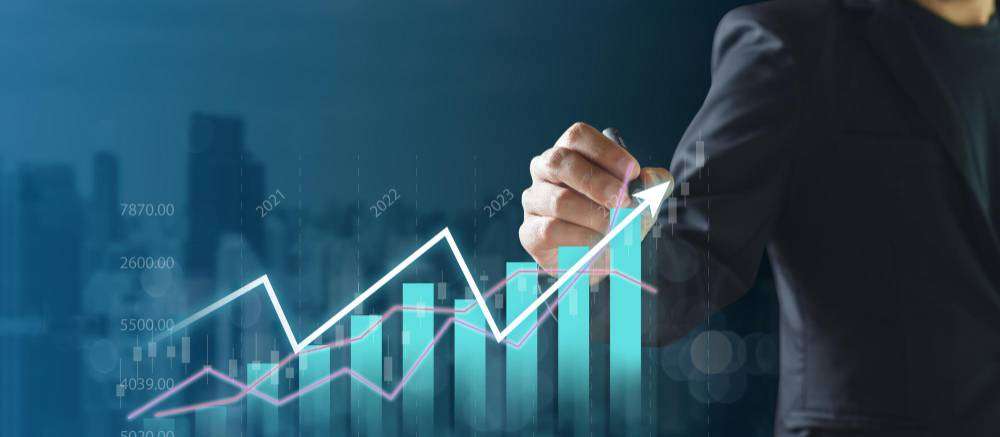
1. Use Inventory Management Software
Benefits:
- Automates inventory tracking, ordering, and reporting processes.
- Provides real-time visibility into inventory levels and movements.
- Enhances accuracy and efficiency in inventory management.
Implementation Tips:
- Choose software that integrates with your existing systems and supports your business needs.
- Train staff on using the software effectively and consistently.
- Regularly update and maintain the software to ensure optimal performance.
2. Conduct Regular Inventory Audits
Benefits:
- Ensures inventory accuracy and identifies discrepancies.
- Detects theft, loss, and damage early.
- Improves overall inventory control and management.
Implementation Tips:
- Schedule regular physical inventory counts, such as annual, semi-annual, or cycle counts.
- Use barcode or RFID technology to streamline the audit process and reduce errors.
- Investigate and resolve any discrepancies promptly.
3. Implement Lean Inventory Practices
Benefits:
- Reduces waste and excess inventory.
- Enhances operational efficiency and responsiveness.
- Supports continuous improvement and cost savings.
Implementation Tips:
- Adopt lean principles, such as the 5S methodology, to organize and manage inventory efficiently.
- Focus on eliminating non-value-added activities and optimizing processes.
- Encourage a culture of continuous improvement and employee involvement in inventory management.
4. Optimize Warehouse Layout and Operations
Benefits:
- Improves inventory accessibility and flow.
- Reduces handling time and costs.
- Enhances accuracy and efficiency in picking and shipping processes.
Implementation Tips:
- Design a warehouse layout that supports efficient storage, retrieval, and movement of inventory.
- Implement best practices for warehouse operations, such as slotting, cross-docking, and batch picking.
- Use technology, such as warehouse management systems (WMS), to optimize warehouse processes and performance.
5. Foster Collaboration Across the Supply Chain
Benefits:
- Enhances visibility and coordination between supply chain partners.
- Improves demand forecasting and inventory planning.
- Reduces lead times and supply chain disruptions.
Implementation Tips:
- Establish strong relationships and communication channels with suppliers, distributors, and other supply chain partners.
- Share demand forecasts, sales data, and inventory information to align planning and execution.
- Collaborate on joint initiatives, such as VMI, collaborative planning, forecasting, and replenishment (CPFR), and continuous improvement projects.
Best Practices for Effective Inventory Control
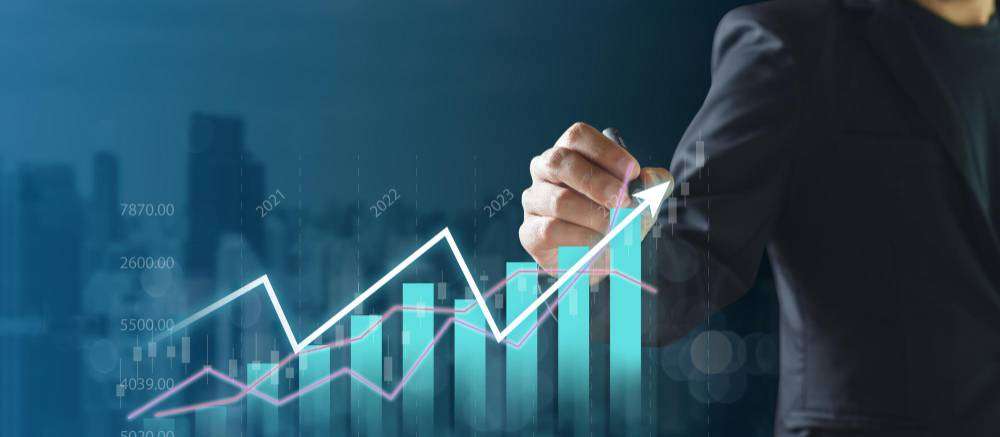
Case Study 1: Toyota’s Just-In-Time Inventory System
Background: Toyota, a global leader in the automotive industry, implemented the Just-In-Time (JIT) inventory system to enhance efficiency and reduce costs.
Strategy:
- Developed strong relationships with suppliers to ensure timely delivery of parts and materials.
- Implemented a pull-based production system where inventory is produced only when there is demand.
- Used kanban cards to signal when inventory needs to be replenished.
Results:
- Significantly reduced inventory holding costs and waste.
- Improved production efficiency and flexibility.
- Enhanced responsiveness to market demand and customer needs.
Case Study 2: Walmart’s Inventory Management
Background: Walmart, the world’s largest retailer, employs advanced inventory management techniques to maintain optimal stock levels and meet customer demand.
Strategy:
- Implemented a sophisticated inventory management system that tracks inventory in real-time.
- Used demand forecasting and replenishment algorithms to ensure products are available when needed.
- Collaborated closely with suppliers through the Retail Link system to share sales data and inventory information.
Results:
- Reduced stockouts and improved product availability.
- Enhanced supply chain efficiency and cost-effectiveness.
- Maintained a competitive edge in the retail market.
Conclusion
Effective inventory control is essential for balancing stock levels and demand, minimizing costs, and ensuring customer satisfaction. By implementing strategies such as Just-In-Time inventory, Economic Order Quantity, ABC analysis, safety stock, reorder points, vendor-managed inventory, demand forecasting, and inventory turnover ratio, businesses can optimize their inventory management processes. Additionally, adopting best practices like using inventory management software, conducting regular audits, implementing lean practices, optimizing warehouse operations, and fostering collaboration across the supply chain can further enhance inventory control and drive business success. By focusing on these strategies and best practices, businesses can achieve a balanced and efficient inventory system that supports growth and profitability.
By prioritizing customer relationships, emphasizing value, and adapting to the evolving needs of the market, businesses can position themselves for sustained growth and success. Remember, sales are not just about transactions; they’re about building long-lasting partnerships that contribute to both customer satisfaction and the bottom line. Through a combination of strategic thinking, interpersonal skills, and data-driven insights, businesses can navigate the complexities of the sales landscape and thrive in the pursuit of revenue growth.