Organizational efficiency is a crucial factor in the success of any business. It refers to how effectively a company utilizes its resources to achieve its objectives and deliver value to its customers. Efficient organizations can operate with minimal waste, maximize productivity, and adapt swiftly to changes in the market. However, achieving and maintaining high efficiency requires constant evaluation and improvement. This blog delves into the importance of assessing organizational efficiency, methods for identifying areas for improvement, and actionable steps to enhance overall efficiency.
Organizational efficiency is not just about reducing costs or increasing output; it’s about creating a balanced approach where resources (including time, money, and human capital) are optimally used to achieve the best possible outcomes. It involves aligning processes, people, and technology to work seamlessly towards the organization’s goals.
Key Indicators of Organizational Efficiency
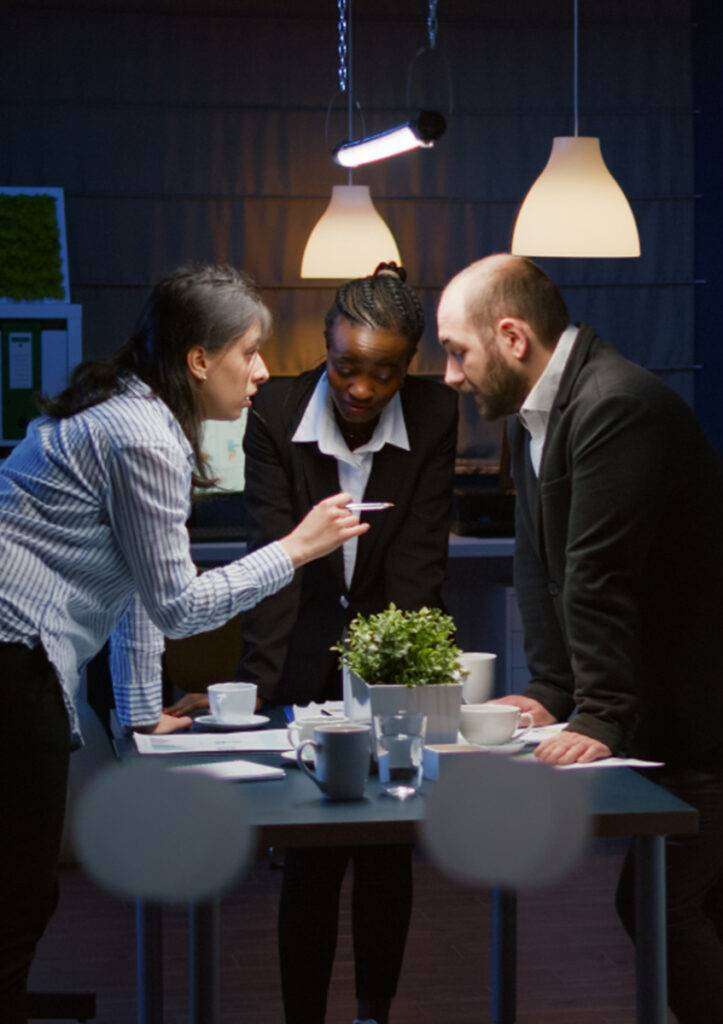
- Resource Utilization: Efficient organizations make the best use of their available resources, whether these are financial, human, technological, or material resources. This includes reducing waste, optimizing processes, and ensuring resources are allocated where they can generate the most value.
- Productivity: This measures the output generated relative to the input used. High productivity indicates that the organization can achieve more with less effort, time, or cost.
- Cycle Time: The time it takes to complete a specific process or deliver a product/service is a critical efficiency metric. Shorter cycle times often reflect streamlined processes and fewer bottlenecks.
- Cost Management: Efficient organizations manage their costs effectively, ensuring they stay within budget without compromising the quality of their products or services.
- Customer Satisfaction: A key indicator of efficiency is how well an organization meets or exceeds customer expectations. High efficiency often correlates with high customer satisfaction, as products and services are delivered reliably, on time, and to the expected quality standards.
- Employee Engagement and Morale: Efficient organizations tend to have motivated and engaged employees who understand their roles and contribute positively to the organization’s objectives. Low turnover and high job satisfaction are indicators of internal efficiency.
Why Assess Organizational Efficiency?
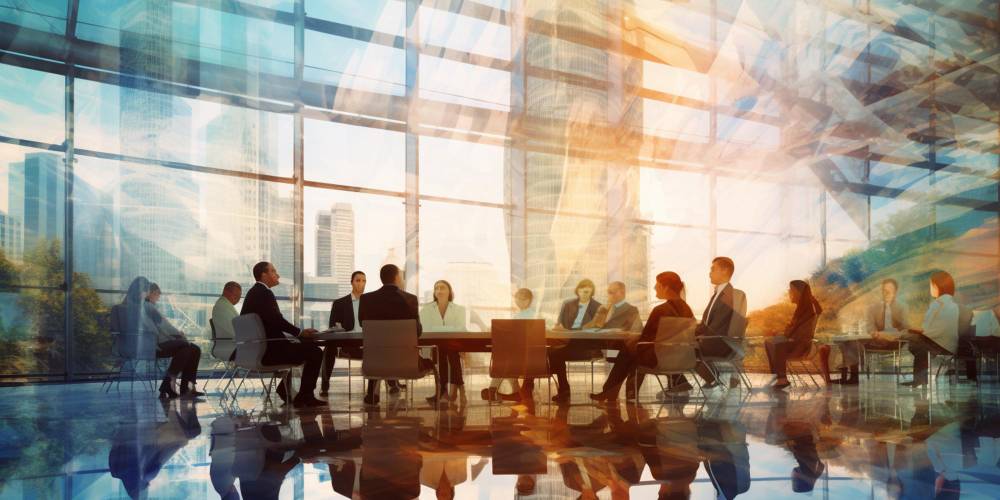
Assessing organizational efficiency is crucial for several reasons:
- Identifying Bottlenecks: Regular assessment helps identify processes that are slowing down operations, causing delays, or leading to wastage of resources. Once identified, these bottlenecks can be addressed to streamline operations.
- Cost Reduction: Efficiency assessments can uncover areas where the organization is overspending or not getting a good return on investment. By improving efficiency, organizations can reduce costs and improve profitability.
- Improving Competitiveness: In a competitive market, efficient operations can be a significant differentiator. Organizations that can deliver high-quality products or services faster and cheaper than their competitors have a competitive advantage.
- Adapting to Change: The business environment is constantly changing. Regular efficiency assessments allow organizations to be proactive rather than reactive, making adjustments as needed to maintain or improve efficiency.
- Enhancing Employee Satisfaction: Efficient organizations provide a better work environment. By minimizing unnecessary workload and stress, they can improve employee morale and job satisfaction, leading to lower turnover rates.
Methods for Assessing Organizational Efficiency
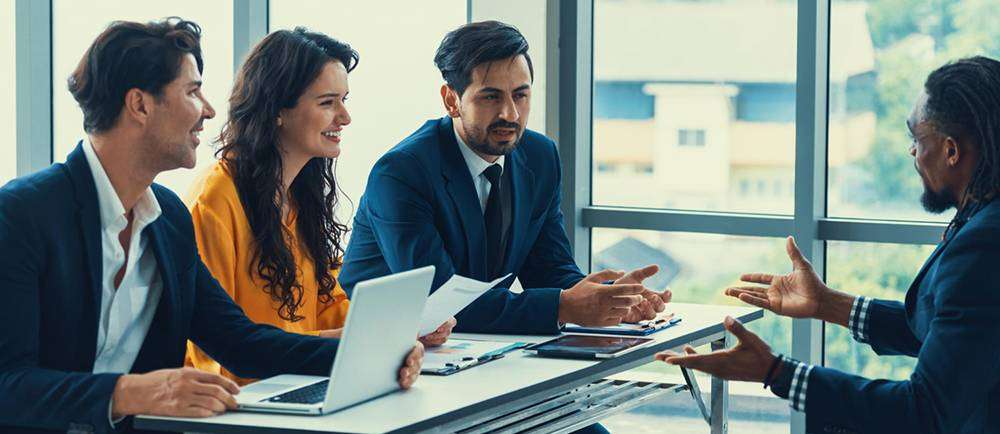
To effectively assess organizational efficiency, a structured approach using various methods and tools is necessary. Here are some commonly used methods:
1. Process Mapping and Analysis
Process mapping involves creating a visual representation of the organization’s processes. By mapping out each step, from start to finish, organizations can better understand how work flows and identify areas where processes may be redundant, inefficient, or causing delays.
Steps for Process Mapping:
- Identify the process to be mapped.
- Gather a team of individuals involved in the process.
- Map out the current process, step-by-step.
- Identify areas of waste, redundancy, or inefficiency.
- Propose changes or improvements to streamline the process.
2. Benchmarking
Benchmarking involves comparing an organization’s processes, practices, and performance metrics to industry standards or best practices. It helps identify gaps in performance and areas for improvement.
Types of Benchmarking:
- Internal Benchmarking: Comparing different departments or teams within the same organization.
- Competitive Benchmarking: Comparing with direct competitors to identify strengths and weaknesses.
- Functional Benchmarking: Comparing with organizations from different industries that have similar functions.
3. Key Performance Indicators (KPIs)
KPIs are specific, measurable metrics that reflect the efficiency and effectiveness of various aspects of the organization. By regularly monitoring KPIs, organizations can track performance and identify areas needing improvement.
Examples of KPIs for Efficiency:
- Revenue per employee.
- Cost per unit produced.
- Customer satisfaction scores.
- Employee turnover rates.
- Average time to complete a project.
4. Employee Surveys and Feedback
Employees are often the best source of information on where inefficiencies lie. Conducting regular surveys and encouraging open feedback can provide valuable insights into operational inefficiencies, communication gaps, and areas where employees feel resources are not being used effectively.
Key Questions to Ask in Surveys:
- What processes or tasks do you find most time-consuming or repetitive?
- Are there any tools or resources you feel would help you do your job more efficiently?
- What barriers do you face that hinder productivity or quality of work?
- How can management support you in improving efficiency?
5. Time and Motion Studies
Time and motion studies involve observing and recording how long it takes to complete specific tasks and identifying unnecessary motions or steps. This method is particularly useful in manufacturing or manual labor environments where physical tasks can be streamlined.
Steps in Time and Motion Studies:
- Select a task or process to study.
- Observe and record the time taken for each step.
- Identify non-value-adding activities.
- Suggest improvements to reduce time and effort.
6. SWOT Analysis
SWOT (Strengths, Weaknesses, Opportunities, Threats) analysis is a strategic tool that helps organizations identify internal strengths and weaknesses and external opportunities and threats. This analysis provides a holistic view of where the organization stands and areas for potential improvement.
7. Lean Six Sigma
Lean Six Sigma combines Lean manufacturing principles, which focus on reducing waste, with Six Sigma’s emphasis on reducing variation and improving quality. Using this approach, organizations can systematically improve processes and eliminate inefficiencies.
Lean Six Sigma Tools:
- DMAIC (Define, Measure, Analyze, Improve, Control): A data-driven improvement cycle used for optimizing and stabilizing business processes.
- 5S Methodology: A workplace organization method (Sort, Set in order, Shine, Standardize, Sustain) that improves efficiency by organizing the work environment.
Identifying Areas for Improvement
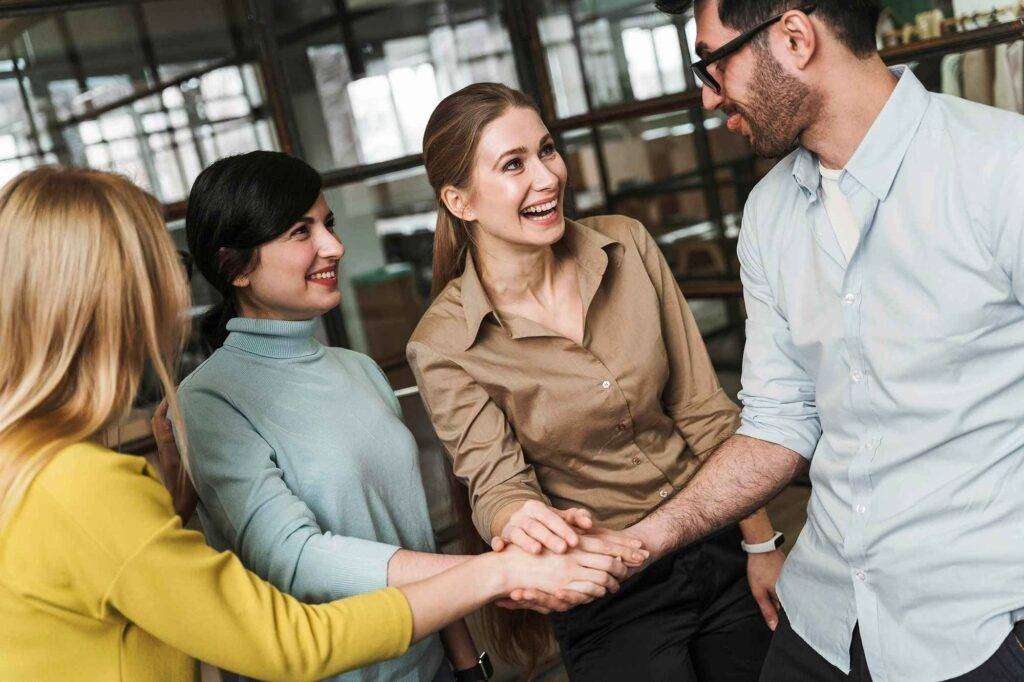
Once you have assessed organizational efficiency using the methods above, the next step is to identify specific areas for improvement. Here are common areas where inefficiencies often exist and how to address them:
1. Process Inefficiencies
Processes that are too complex, have too many steps, or involve unnecessary approvals can slow down operations. Process mapping can help identify these inefficiencies. Simplifying processes, eliminating unnecessary steps, and automating routine tasks can improve efficiency.
2. Communication Breakdowns
Poor communication can lead to misunderstandings, errors, and delays. Identifying areas where communication is lacking, such as between departments or teams, and implementing better communication channels can enhance efficiency. Regular meetings, clear reporting lines, and collaborative tools can facilitate better communication.
3. Technology Gaps
Outdated or incompatible technology can hinder productivity. Conducting a technology audit to identify gaps and investing in modern, integrated systems can streamline operations and improve efficiency. Ensure that employees are trained to use new technologies effectively.
4. Resource Allocation
Inefficient allocation of resources, whether it’s underutilized employees or overspending on materials, can impact efficiency. Regularly reviewing resource allocation and making adjustments based on current needs can ensure that resources are used optimally.
5. Waste Reduction
Lean principles focus on reducing waste, whether it’s time, materials, or effort. Identifying areas where waste occurs, such as overproduction, excess inventory, or unnecessary movements, and implementing strategies to reduce waste can improve efficiency.
6. Employee Training and Development
Employees who are not adequately trained or lack the skills needed for their roles can contribute to inefficiency. Regular training and development programs can enhance employee skills, improve job performance, and contribute to overall organizational efficiency.
7. Decision-Making Processes
Lengthy decision-making processes can slow down operations. Assessing how decisions are made within the organization and finding ways to streamline these processes can improve efficiency. Empowering employees with the authority to make decisions within their roles can also speed up decision-making.
8. Customer Feedback
Listening to customer feedback can provide insights into areas where the organization is not meeting expectations. Regularly reviewing customer feedback and making necessary adjustments to products, services, or processes can improve efficiency and customer satisfaction.
Implementing Improvements
Identifying areas for improvement is only the first step. Implementing changes requires careful planning and execution. Here are some steps to effectively implement efficiency improvements:
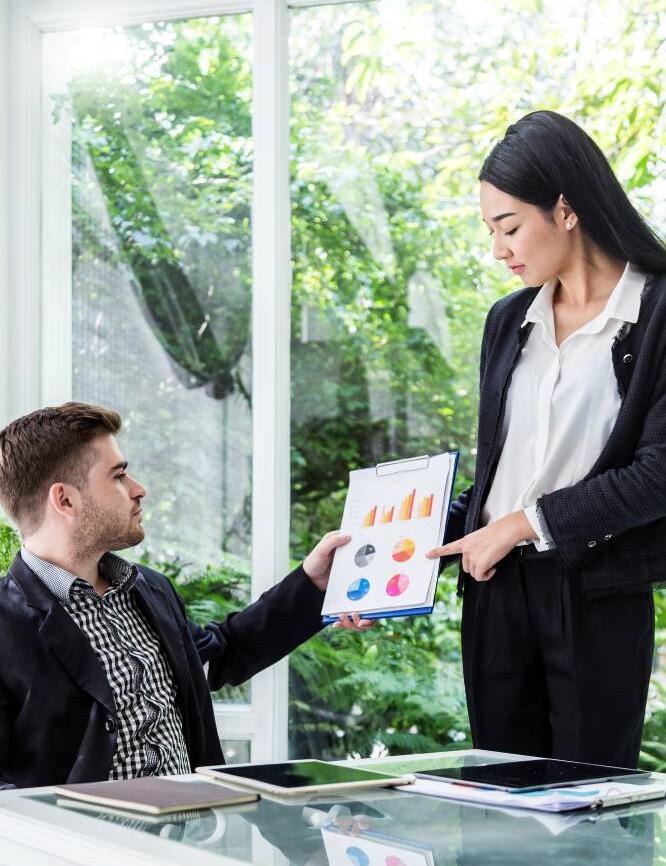
1. Set Clear Objectives
Define clear, specific objectives for what you want to achieve with the efficiency improvements. Objectives should be measurable and aligned with the organization’s overall goals.
2. Develop an Action Plan
Create a detailed action plan that outlines the steps needed to achieve the objectives. Assign responsibilities, set timelines, and allocate resources. Ensure that everyone involved understands their role and what is expected of them.
3. Communicate Changes
Effective communication is crucial when implementing changes. Communicate the reasons for the changes, the benefits, and how they will impact the organization. Engage employees and involve them in the process to gain their support.
4. Monitor Progress
Regularly monitor the progress of the improvements. Use KPIs and other metrics to track performance and identify any issues early. Make adjustments as needed to stay on track.
5. Evaluate Results
Once the improvements have been implemented, evaluate the results against the objectives. Assess whether the changes have led to the desired improvements in efficiency. Use this evaluation to identify further opportunities for improvement.
6. Continuous Improvement
Efficiency is not a one-time effort but an ongoing process. Encourage a culture of continuous improvement where employees are always looking for ways to do things better. Regularly review and refine processes to maintain and enhance efficiency.
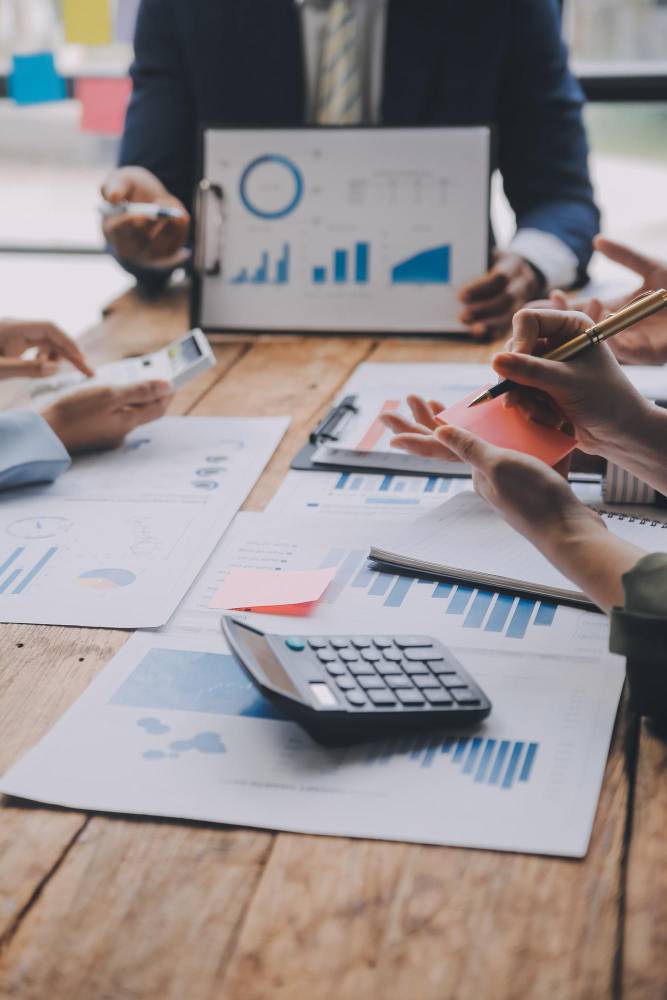
Conclusion
Assessing organizational efficiency is critical for identifying areas for improvement and ensuring the long-term success of any business. By using a structured approach to assess efficiency and implementing targeted improvements, organizations can reduce waste, enhance productivity, and achieve their goals more effectively. Embracing a culture of continuous improvement, where efficiency is a constant focus, will position organizations for success in today’s competitive business environment.